Overview
Additive Flow makes it simple to harness the potential of additive manufacturing – as exemplified by this collaborative project with Royal HaskoningDHV and DSM — by optimising the design and production workflow; in this case for high value, large scale additive manufacturing.
Project
Additive Flow worked with Royal HaskoningDHV and DSM to deliver a next-generation 3D printed bridge design. Royal HaskoningDHV is a leading independent and global engineering and project management consultancy. One of the core values of Royal HaskoningDHV is sustainable development and innovation. To this end, the company is leading the way in digital engineering design and its application to 3D printed structures and is able to bring more than a century of civil engineering excellence and expertise to bear on its more recent focus on using additive manufacturing processes to build bridges.
DSM has a wealth of experience in developing engineering materials. In terms of additive manufacturing and 3D printing, DSM was one of the pioneering companies driving the growth of this sector more than 25 years ago and continues to innovate today with the development of new performance materials and accumulated application expertise with which it supports manufacturers that have adopted or are adopting additive technologies for more sustainable production. DSM also delivers ecosystem wide initiatives to promote collaboration and partnerships that unlock the potential of additive manufacturing. This was the purpose of the ‘I AM Tomorrow’ initiative, which enabled this collaborative project.
Over the course of a year, Royal HaskoningDHV had developed and built a manual workflow for 3D printed bridge design, and were looking to increase efficiency through optimised design workflows, optimised material use, and increase light-weighting opportunities. The specifics of this project involved running an advanced multi-property topology optimisation on the design domain of a pedestrian bridge, that was to be 3D printed with a large scale pellet printer and a high performing fibre reinforced polymer from DSM.
Additive Flow was brought in to collaborate on this project, and apply its Formflow software to enable an efficient scalable workflow for optimising the design in a number of key — and unique — ways.
Objectives
- Reducing product development from months to days.
- Deploying Additive Flow’s advanced structural multi-property solvers that are orthotropic and additive aware to enable an efficient scalable workflow for optimising design and production.
- Improving material property allocation and overall functionality of the part.
- Adaptive latticing for enhanced light weighting without compromising functionality.
Why Additive Flow
Additive Flow deployed its ground-breaking Formflow software and three key features in particular were brought to bear on this project.
ˋAdditive-Awareˊ Solvers – Anisotropic Optimisation:
We were able to produce a detailed study showing that orthotropy counts, with the same design domain and load cases, to compare results for:
- Isotropic parameters
- Orthotropic parameters (printed upright)
- Orthotropic parameters (printed sideways)
Additive Flow worked with DSM’s material experts to ensure material models were accurate and matched empirically validated models.
We were also able to demonstrate the differences between solid topology, manual homogenous properties, and adaptive properties and produce a direct comparison. This was achieved by working directly with Royal HaskoningDHV’s experienced engineering team to embed their years of insight within the optimization.
Streamlined Multi-Property Production
We deployed our efficient user-friendly interface to enable a multi-property workflow, where different build parameters could be applied as per local functionality requirements of the part. This unlocks productivity, cost, and performance improvements vs. traditional manufacturing by eliminating the time consuming complexity of manually deciding which regions should have which property sets.
This is where Additive Flow’s Multi- Property optimisation algorithms came into their own for this project and our software was able to address the different parameter sets within each optimization. This was achieved by working with RHDHV’s wealth of application engineering data and empirically tested expertise on different scenarios which was then allocated by Additive Flow’s optimizer.
Workflow Friendly
We play nice with other AM ecosystem companies, whereby for this project high resolution, data-rich file format exports were easily produced for deployment within the existing tool-chain at Royal HaskoningDHV. As such, a simulation-ready mesh was produced and our highly performing results were validated by leading simulation experts. We were also able to generate split mesh production files for ready deployment of multi-property print parameters by the build-processor software. This highlighted further lightweighting and optimization opportunities, saving time, money, and unlocking further efficiencies in this high value application for AM.
Results
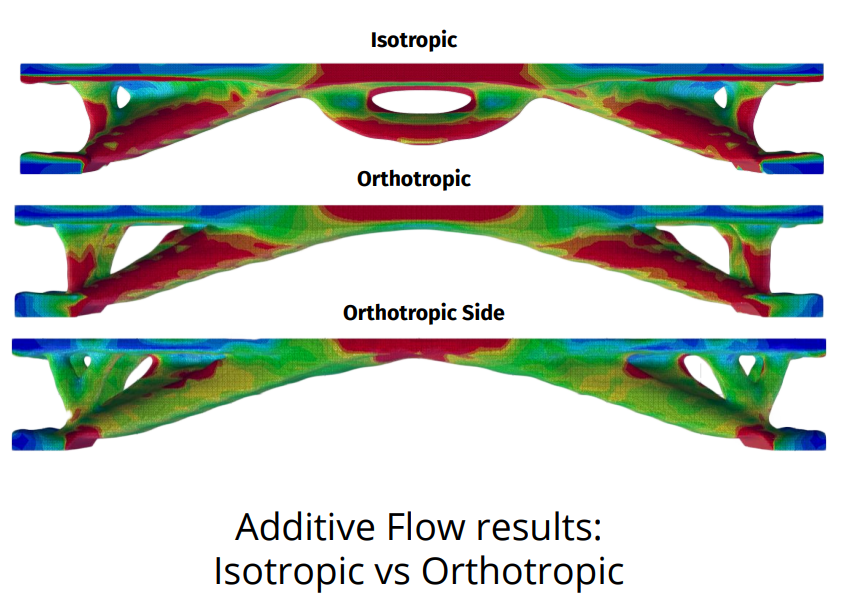
Isotropic Versus Orthotropic | 17% lighter (3% less max stress) |
Isotropic Versus Orthotropic Side | 9% lighter (23% less max stress) |
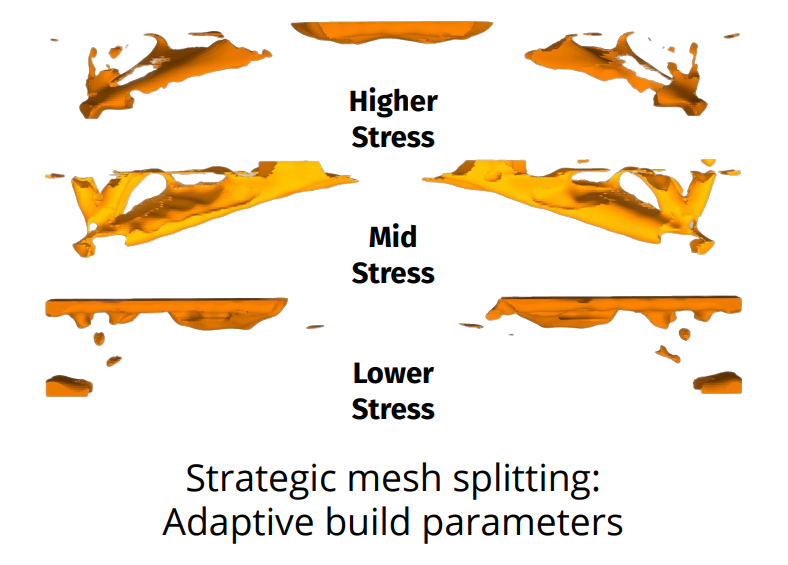
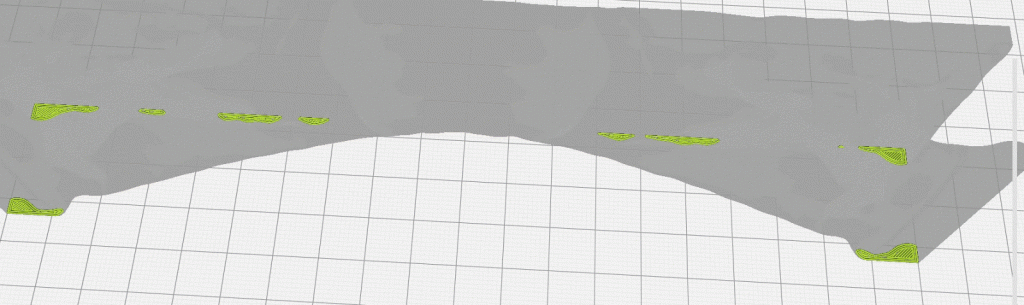
Summary of Results
- Improved weight reduction:
- Additive Flow’s optimised model was 7 x lighter than the solid volume. Deploying our orthotropic solvers resulted in a 20% better optimisation isotropic approach,
- Additive Flow’s optimisation resulted in a further 13% improvement versus manual iterations from Royal HaskoningDHV.
- Workflow Improvement
- Additive Flow’s applications engineers set up a repeatable workflow in days vs. months, and delivers advanced optimisations in minutes.
- Additive Flow’s Formflow reduced complexity by making multi-parameter allocation straightforward and data-driven.
- Sustainability
- 3D Printing Additive Flow’s optimised bridge with DSM’s Arnite would be 10x more sustainable LCA than concrete construction, 15x more sustainable LCA than steel construction
Testimonial
“Royal HaskoningDHV has tried a wide range of topology optimization software to benefit from the freedom structural 3D printing has to offer. Pre-existing tools were limited to single material properties, and only allowed for isotropic behaviour. This meant generatively designed bridge outcomes were not structurally feasible or possible to produce.
Additive Flow’s software brings new capability to deliver the potential of additive – specifically optimising for orthotropic materials, and the ability to allocate multi properties through a product is game changing. We can now allocate different material properties in tension and pressure zones, and further optimize with multi directional behaviour. Advanced manufacturing has now become more feasible for the civil industry. Working with Additive Flow’s enthusiastic and expert team has been very positive, and they have delivered impressive results in an innovative way. I am very excited to see where this is heading.”
Kees van IJselmuijden
Senior Civil Structural Engineer, Manager Digital Engineering
Royal HaskoningDHV